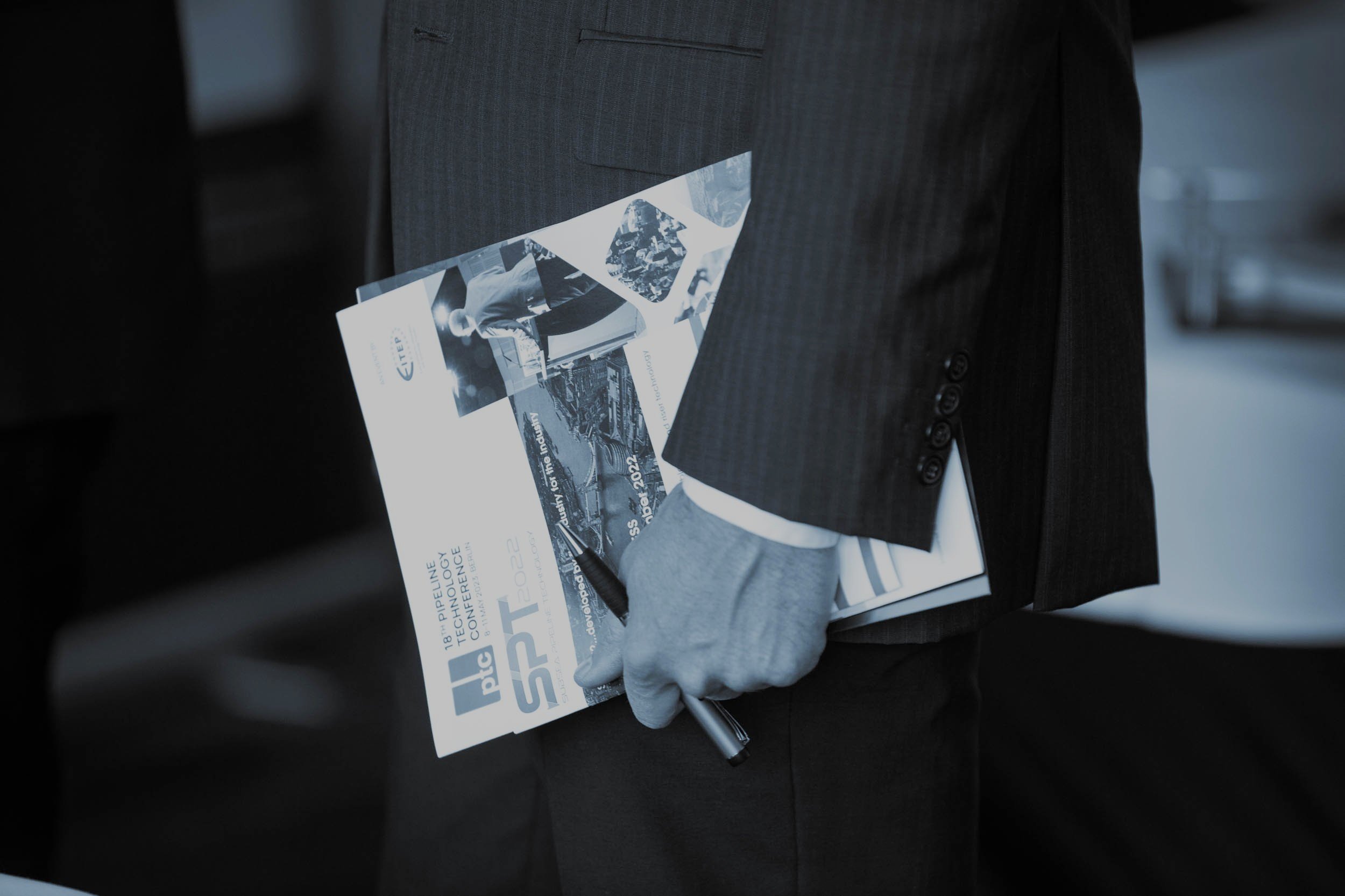
Agenda
SPT 2024 Congress
Leonardo Royal Hotel
London Tower Bridge
DAY 1: Wednesday 23 October 2024
08:00
Registration and coffee
09:00
Welcome to SPT 2024
Steve Woolley, Director, SW Conferences Ltd
09:05
Welcome from the session chair
Pieter Swart, Director and Pipeline Authority, SeaLeopard Engineering
SESSION 1: GLOBAL ENERGY OUTLOOK AND OFFSHORE PIPELINE MARKET UPDATE
09:10
Global energy outlook and implications for the offshore pipeline sector
Mark Adeosun, Director SubseaLogix and PlatformLogix, Westwood Global Energy Group
09:35
Keynote address A contractor’s view of the global offshore pipeline market
• Market analysis and impact on the contractor community
• Operating in a transitioning market, meeting new demands
• New approaches and solutions to achieve enhanced cost efficiencies and greener operations
• A look to the future
Dario Li Gioi, Head of Strategy and M&A, Saipem Group
10:00
Keynote address CO2 Highway Europe: A game changer in energy transition
Grethe Malene Sagerup, Project Director CO2 Highway Europe, Equinor
10:25
Networking break
SESSION 2: HYDROGEN AND CO2 PIPELINES
11:00
CO2 pipeline safety, design, and operations: what are the differences from a natural gas pipeline?
Speaker: John Willcocks, Technical Consulting – Technical Director Oil & Gas, Wood
-
Overview of safety regulations
Typical hazardous area, land use planning and Qualitative Risk Assessment (QRA) outcomes
Impact of safety on the routing and facility layout
What are the code requirements for CO2 pipelines
What are the CO2 specification inlet requirements?
How do the mechanical design requirements for CO2 pipelines differ from natural gas lines?
How do the line pipe requirements differ from natural gas line pipe?
What are the CO2 compressor requirements and TRL.
Implications of CO2 service on integrity management and operations
Discuss of impact on requirements for corrosion management, crack development, flanged connections, ESD, valves, inline inspection, SCADA and third party interaction
Inspection, Maintenance and Repair (IMR) technology gaps
11:30
Repurposing onshore and offshore pipelines for hydrogen transport
Speaker: Alfons Krom, Material Integrity Specialist, N.V. Nederlandse Gasunie
Authors: O.J.H. Wesselink, A.H.M. Krom and Pieter Swart, Gasunie
-
The Dutch government has set targets for the growth of offshore wind energy production at 50GW in 2040 and 70GW in 2050. In the letter to Parliament on offshore wind energy 2030-2050, the cabinet has announced that hydrogen production at sea is necessary for the successful and steady growth of offshore wind energy. To unlock the value of hydrogen production at sea, an offshore hydrogen network is needed, consisting of offshore electrolysis, compression stations, offshore pipelines, integration into the onshore network, and other electricity and energy infrastructure. At the same time importation of blue hydrogen may play an important role as well, especially in the early phase of the offshore network. In the HyOne project, Gasunie, the Dutch operator for Hydrogen en Natural Gas, is presently assessing the feasibility of an offshore hydrogen network, whereby various options are evaluated, including new built and potential reuse of existing pipelines. This paper outlines Gasunie's assessment, ensuring that repurposed pipelines meet integrity requirements and can be operated safely, both for onshore and offshore applications. This assessment is grounded in preventing the degradation mechanism known as hydrogen-enhanced fatigue defect growth. It entails effectively managing pressure variations or other fatigue loads to hinder the growth of pre-existing planar defects within the pipelines. The primary locations susceptible to these defects are the welds in the line pipes and the girth welds of the pipelines. The specific defects to evaluate depend on the type of fatigue loading involved. Once the service life, fatigue load type, and the types and sizes of defects are established through comprehensive study, the permissible fatigue load can be computed. This calculation is founded on a restricted degree of defect growth.
12:00
Carbon fibre reinforced PA12 thermoplastic composite pipes for CCS applications: opportunities and challenges
Speaker: Frans Janssen, Production Development Manager, Strohm
-
The current operating envelope and track record of CF-PA12 TCP’s
What’s new: specific aspects of CO2 service and CCS applications
PA Hydrolysis, effect of contaminants in CO2 stream, rapid gas Decompression, phase transitions and temperature changes
Required and ongoing TCP qualification for CCS applications
12:30 Networking lunch sponsored by
Session Chair
Venkatapathi Tharigopula, Concept Manager – Trunklines, Equinor
SESSION 3: NEW PIPELINE TECHNOLOGIES AND MATERIALS
13:30
Flow assurance simplification through electrical heating of a flexible production riser with emphasis on thermal efficiency and operational robustness
Speaker: Thorsten Holst, Senior Development Engineer, NOV – Subsea Production Systems, Flexible
Authors: Thorsten Holst and Casper D. Hansen, NOV Subsea
-
This paper describes a fully qualified direct electrical heating method, which offers unique flow assurance opportunities in flexible riser systems used for subsea oil and gas production. The carcass of the flexible pipe is used directly as the electrical heating element, which offers a highly effective way to heat up the bore content. This enables simplified subsea field architecture, significant environmental benefits (and cost savings) by avoiding abundant infrastructure, and thereby improves the business case for both brownfield extensions and greenfields. A thermal model of the flexible riser is used to calculate the electrical power required to ensure the desired thermal control dictated by flow assurance requirements.
We will present the different building blocks of the topside AC power system and how these units can be designed to form a compact system. The electrical power is fed to the riser, where power connectors are integrated in the EX-approved topside end fitting. Optical fibers are embedded in the tensile armour layer of the riser and are used to monitor the riser temperature and provide feedback for the power regulation system.
We outline the electrical model of this heated pipe power system to present a case study with parameters descriptive of a realistic flexible riser installation. We use this model to highlight the robustness of some anticipated operational conditions, such as the case of an outer sheath breach and the presence of conductive formation water inside the bore. The operational philosophy includes all aspects of safety functions.
14:00
Alternative CRA Alloys for MLP liner fabrication
Speakers: Rodrigo Signorelli, Lead Technical Manager – Marine & Energy, Outokumpu and Tiago Kaspary, Engineering Director, Cladtek The Americas
Authors: Rodrigo Signorelli, Tiago Kaspary, Ahmed Reda, Jessica Pisano, Suryanarayanan
-
Mechanically Lined Pipe (MLP) is an enabling technology for the development of corrosive oil and gas fields, as well as for associated applications such as CCUS. Besides the technical and sustainability aspects, one fundamental advantage of MLP to its traditional alternative, Metallurgically Clad Pipe, is its cost-effectiveness and greater availability. Current projects however do not fully explore the potential of MLP and the wide range of corrosion resistant alloys (CRA) that could be used to optimize project economics while remaining suitable for specific field conditions. Particularly in the Brazilian Pre-Salt reservoir, Alloy 625 has been the alternative of choice since its precursor project Guara and Lula. It has been applied ever since, even though PETROBRAS has recently indicated conditions that would allow for the alternative CRA to be used in some applications.
This work explores the application of 254SMO (UNS S31254 / EN 1.4547) and 654SMO (ASTM UNS S32654 / EN 1.4652) as alternative liner materials for MLP fabrication. 254SMO is a consolidated material used in a number of offshore applications including high responsibility systems, as fire suppression with seawater, and heat exchangers, where seawater is used as coolant. It has presented with good weldability, excellent resistance to pitting and crevice corrosion and high resistance to stress corrosion cracking thanks to its high nickel content. 654SMO increased alloy content, particularly N and Mo, results in PRE exceeding 56, CPT > 90oC and CCT > 60oC, surpassing the staple Alloy 625. Both alloys enable significant savings on the cost of MLP, while allowing for a wider range of suppliers and CRA availability.
Cladtek has manufactured liners and MLP with the combination of DNV450(X65) carrier pipes with 254SMO and 654SMO supplied by Outokumpu/Nyby. The results of the qualification programs are summarized herein. Other potential candidate alloys for MLP application and future developments are also discussed.
14:30
Networking break
SESSION 4: DESIGN CONSIDERATIONS (PART I)
15:00
The feasibility of challenging projects using unrealistic design scenarios
Speaker: Joost Brugmans, Project Manager, Worley Offshore Energy
Authors: Rui Rodrigues, Joost Brugmans, Jeroen Timmermans - Worley Offshore Energy
-
The demand for larger-and-deeper subsea pipelines has led our industry to push the limits for pipeline design, with particular focus on increasing collapse resistance. These developments have resulted in improved material and fabrication aspects, design formulations and availability of record-breaking installation assets. However, the criteria suggested/required by design codes and operator standards in early-phase desktop and feasibility studies, are not always in step with these developments.
This paper highlights how early-phase design criteria and design scenarios can result in a negative conclusion regarding project technical feasibility before the latest technology developments are given due consideration. This paper presents experience from ‘real projects’ where we have studied feasibility of relatively large diameter (24-28 inch) pipelines in up to 3,000 meters water depth. On some occasions, the technology limits of fabricability are allowed and required to be fully explored while maintaining early phase installability criteria that ignores installation capabilities of today, thus negating the gains of the ‘cutting-edge’ materials and fabrication aspects. In other cases, unrealistic conservatism (albeit well intentioned) in assumed operating conditions will lead to too thick pipes, making them ‘too strong to be installed’ (i.e. too heavy), especially if ‘dated’ installation criteria is prescribed.
These criteria, in design codes and operator standards, surely have had a purpose and a historical context that is not explicit in the way they are redacted in present editions. Without compromising safety, the existing criteria could do well with adjustments or clarifications to accommodate the technological gains achieved by the industry
15:30
Talbot and Affleck: Design of buried reeled pipe in pipe systems
Speaker: Chris Cooper, Technical Authority – Rigid Pipelines, TechnipFMC
Authors: Chris Cooper, TechnipFMC - Brian Molloy, Harbour Energy and David Kaye, TechnipFMC
-
The Talbot development project and the Affleck re-development project were executed as a combined single iEPCI. Both projects adopted a reeled pipe in pipe (PIP) system to transport hydrocarbons to the host platform. Because of the moderately high design temperatures and the inherent residual bending moment in the reeled pipe in pipe system, a strain-based design philosophy was adopted to verify the integrity of the inner flowline of these buried PIP systems. The residual bending moment arises because of the effects of plastic strain during reeling and is characterised by a self-equilibrating (opposing) moment between the two pipes. This residual bending moment may potentially interact with applied operational loads and modify the design limit states for the PIP.
The method of analysis presented in this paper has been adopted on many projects but is not widely documented in the public domain. This is addressed by providing a summary of the work undertaken on both the Talbot PIP system and the Affleck PIP system. The approach complies with the design recommendations in the commentary of DNV-ST-F101 and highlights how the residual bending moment in the inner flowline and outer carrier pipe in a pipe-in-pipe system can be considered for in-place design. In conclusion, this paper shows that the impact of residual bending moment on the integrity of a reeled and buried PIP system is negligible.
16:00
Case study to investigate the application of DNV-RP-F105 to flexible pipeline, umbilical and cable
Speaker: Linlin Jiao, Principal Engineer, DNV
Authors: Linlin Jiao, Principal Engineer and Mário Caruso, Principal Engineer, DNV
-
Free spans on slender subsea structures on the seabed such as pipeline, umbilical and power cable might develop due to various reasons, e.g., seabed unevenness, scouring, crossing and end terminations, etc. Free spanning of these type of subsea structures is a typical concern of ensuring their integrity against static loads generated by seabed roughness, functional loads induced by internal temperature and pressure (if any), and environmental loads due to waves and currents. One of widely used methodology for free span design is according to DNV-RP-F105 Free spanning pipelines. This recommended practice presents models to predict the loads induced by dynamic environmental loads due to Vortex Induced Vibration (VIV) and direct wave action. DNV-RP-F105 was developed for rigid pipelines. Due to lack of direct guidance for free spanning of a non-rigid pipe on the seabed such as flexible pipeline, umbilical and cable, the industry also applies it to these structures. In this paper, the application of DNV-RP-F105 to flexible pipeline, umbilical and cable is investigated through case studies. The fatigue assessments are performed through FatFree, DNV developed software in compliance with DNV-RP-F105. The recommended practice applications and different modelling choices are introduced and discussed.
16:30
Chairman’s closing remarks
17:45
Interactive roundtable session
This session will provide an informal environment for delegates and speakers to come together to discuss and debate those issues currently influencing their business. Each table will be moderated by a leading expert and delegates choose which table to join:
Table 1: CO₂ pipelines in the energy transition
Moderator: Phil Cooper, Aramis FEED Project Director, Petrofac
Table 2: Hydrogen pipelines
Moderator:
Table 3: Energy security and what role can pipeline projects play?
Moderator: Tim Crome, Chief Engineer, TechnipFMC
17:45
Close of Day 1 followed by Networking Drinks Reception sponsored by
19:30
SPT Gala Dinner
DAY 2: Thursday 24 October 2024
SESSION 5: INSTALLATION
08:30
Registration and coffee
09:00
Welcome from the chair
Carlos Sicilia, Head – Rigid Pipe and Riser Design Group, TotalEnergies
09:10
A novel approach to retrofit riser installation
Speakers: Ian Nash, Group Managing Director and Chas Spradbery, Director of Operations and Business Acquisition, Peritus International
-
In 2021 Peritus was responsible for the retrofit riser design of 4 CRA Clad risers in 55m WD for installation on a battered jacket face well underneath the topsides structures. The proposal for these risers from FEED was problematic, so Peritus developed a novel design and installation approach that significantly improved the speed of installation and risk profile. The presentation will cover:
• Initial design and resulting construction issues
• Alternative design optimised for installation
• Final construction case study
09:40
Analyses and verification of J-Tube pull-in for pipe-in-pipe rigid flowlines
Speaker: Yi Yu, Senior Principal Engineer, Subsea 7 Norway
Authors: Yi Yu, Kristen Rege and Sangga Ciptadi, Subsea 7
-
The J-tube pull-in installation method has been used for connecting subsea pipelines to platform topsides in North Sea. When a rigid riser is pulled through a J-tube bend, there will be a large bending moment in the riser and large reaction forces on the J-tube. The J-tube bend will also lead to a very high pull-in force when the riser bending stiffness is high, especially for pipe-in-pipe (PiP) rigid risers.
In this paper, the pull-in analysis and the subsequent result validation from installation for a challenging J-tube pull-in project with 10”/14” PiP rigid riser are presented. Initially, the analysis method using beam elements with tube-to-tube contacts in finite element modelling to simulate the pull-in process is presented. Secondly, as the topside structure, the J-tube and the J-tube secondary structure must be able to resist the pull-in load and reactions from the heavy PiP riser, measures to reduce the pull-in force and to optimize the analyses are discussed. With these measures, the predicted maximum pull-in force was successfully reduced to below capacity. The approaches to reduce the loads acting on the J-tube is discussed next, since the integrity of the J-tube and the structures must be guaranteed during the pull-in. The proposed solutions to reduce those loads are checked and verified subsequently. Finally, the seal installation method is described and the required seal installation loads are estimated. The analysis shows the seal can be installed by the proposed method. In the subsequent offshore campaign, the rigid PiP riser was pulled into the J-tube without damaging the J-tube or the secondary structure and the seal was installed successfully. The predicted pull-in force matches well with the on-site measurement. Therefore, the J-tube pull-in analysis methodology is verified, and the effectiveness of optimization measures are demonstrated.
10:10
Pipelines for superconducting cables: advances in the qualification of a solution
Speaker: Christian Geertsen, R&D Manager, ITP InTerPipe
Authors: C. Geertsen, A. Damour, ITP InTerPipe, L. Quéval, GeePs, CentraleSupelec, Université Paris-Saclay
-
Superconducting cables can provide a cost-efficient transmission link for the electrical power generated by offshore wind farms. Operating at higher current and lower voltage than conventional transmission cables, enables significant savings on the transformer stations.
Superconducting cables need to be cooled to cryogenic temperature to achieve zero electrical resistance. This is obtained by hosting the cables inside well-insulated pipelines through which liquid nitrogen (LN2) is circulated to maintain the transmission link at ca. -200°C. Such a pipeline could be installed by reeling or towing.
While the physics of such a system are relatively straightforward, the qualification and construction require a significant effort from companies across different industries. A consortium of significant players has been set up to address these challenges. These include Nexans, Air Liquide, ITP, Univeristé Paris-Saclay and RTE as a core. Each has a recognized expertise in its own areas and has a reputation for excellence (superconducting cables, cryogenics, pipe-in-pipes, electrical engineering and power transmission).
The paper will briefly describe the technology and its economic rationale. It will then identify the main challenges and how these will be addressed within the framework of the cooperation. Use cases are currently focussed on the French market but can be applied to other sites.
10:40
Networking break
SESSION 6: DESIGN CONSIDERATIONS (PART II)
11:10
Balancing act: Navigating residual lay tension in subsea pipeline design
Speaker: Sean Murray, Pipelines Team Leader, Lloyd’s Register
Authors: Sean Murray, Sameer Chapgaon, Scott McAllan and Vynx Lim, Lloyd’s Register
-
The level of residual lay tension which should be considered in the design of a subsea pipeline has long been a topic of debate within the industry. The debate centres around the degree of conservatism to apply when considering residual lay tension in various design aspects. Take, for instance, the assessment of global buckling. The assumption of low levels of residual lay tension is often seen as conservative as this maximises the compressive axial force in the pipeline under operating conditions. However, if a high level of buckle reliability is required, the assumption of low levels of residual lay tension may result in an overestimation of the real buckle formation reliability.
There is no question that, during installation, pipelines are subjected to large levels of tension and to maintain equilibrium residual lay tension in the on-seabed pipeline must be present during installation. Nevertheless, estimating the appropriate level to use for design is neither clear nor straightforward. Although industry guidance acknowledges the uncertainty surrounding residual lay tension, it does not provide guidance on how much residual lay tension can be lost or the mechanisms by which this loss can occur.
This paper presents a literature review on this topic and summarises the mechanisms by which residual lay tension can be lost. The paper also presents results of parametric studies which investigate the effect of these mechanisms, such as lateral pipe movement, to quantify the levels of residual lay tension which may be lost.
11:40
Upheaval buckling of buried pipelines – What do we really know?
Speaker: John Canney, Rigid Pipeline Engineering Portfolio Manager (EMIAA), TechnipFMC
Authors: John Canney and Chris Cooper, TechnipFMC
-
Upheaval buckling (UHB) of buried pipelines has been extensively studied for over thirty years. As computer hardware has advanced so have our assessment tools. Post installation survey data appears to have improved dramatically in recent years and industry recommended practices have matured. Our ability to quickly undertake several sensitivity studies in the short time frame between survey and rock dump means that, in theory, a more refined rock placement table can be produced. But with all these technology improvements are our UHB designs any better? Do buried pipelines still buckle in operation? Why are the safety factors for UHB often high? Does our predictive UHB design provide a good estimate of required rock volume? In other words, what do we really know about UHB and what assumptions are hidden within the methodology?
This paper attempts to answer some of these questions by using a few case studies as examples. It provides a summary of some recent challenges on buried pipeline upheaval buckling design. It also takes a critical look at the input data used in the analysis. In other words, it attempts to distinguish between what we know and what think we know. Finally, recommendations are given for development opportunities that could lead to improved UHB design and hopefully, reduce project cost
12:10
Pipelines that move with all six degrees of freedom – Lessons from walking and lateral buckling interaction of subsea pipelines
Speaker: David Bruton, Senior Advisor, Crondall Energy
Author: David Bruton, Senior Advisor, Crondall Energy
-
Many pipelines laid on the seabed experience cyclic lateral buckling in three dimensions, and walking (stepwise ratcheting displacement along the axis of the pipe). Both mechanisms are caused by shutdown and restart cycles in operation, combined with one or more other driving mechanisms, including: seabed slopes, thermal transients, liquid drop-out, SCR tension, route-curve pull-out, ratcheting lateral buckles, and berm-encroachment at lateral buckles.
All these mechanisms have been observed on operating pipelines. However, predicting the rate of walking and pipe behaviour in the design phase remains extremely challenging due to inherent uncertainties in the design. Chief amongst these are: (1) pipe-soil interaction under cyclic loading; (2) the uncertain operating temperature and pressure cycling, which will vary over time; (3) the installed condition, including levels of residual tension. This uncertainty has led to projects installing high-capacity anchors, typically of 100t or more to arrest walking - should it occur. The design approach also varies significantly from project to project and operator to operator.
Many pipelines do not walk, but those that do can present significant integrity management challenges. Lessons learned from back analysis of operating pipelines to quantify and explain the walking mechanism and rate of walk has led to a growth in understanding and experience that has helped to identify newly observed contributory mechanisms to pipeline walking. There are still lessons to be learned from the monitoring and observation of pipeline systems that behave well, and those that do not.
Alongside this work, more efficient anchoring systems have been developed that can be retrofitted and allow the adoption of delayed intervention wherever possible, in what has become known as the “wait and see” approach (Observational Method). This approach is based on improved methods for continuous monitoring of pipeline walking to predict future response, and innovative retrofit anchoring solutions that limit unnecessary mitigation costs and avoid mis-placed anchors.
While operating regimes will always be difficult to predict, not helped by conservative flow-assurance predictions, work has progressed in other important areas: (1) the monitoring of pipeline walking with the pending installation of a WMS (Walking Monitoring Sensor). (2) much improved understanding of the cyclic soil response based on observations of real behaviour, and (3) the development of full 3D structural PSI modelling of a lateral buckle that compares very well with field observations of pipelines that have been in operation for many years.
12:40
Networking lunch sponsored by
Session chair
Paul Hawkins, Discipline Lead for Pipeline Engineering, Global Projects, BP
SESSION 7: INTEGRITY MANAGEMENT
13:40
Key observations and insights from long-term deepwater pipeline integrity management programme
Speaker: Ramy Magdy, Principal Pipeline Engineer, Petrofac
Authors: Hamza Moustafa and Ismail Zohdy, East Gas Company (EGC) - Philip Cooper, Kevin Williams and Ramy Magdy A. Mahmoud, Petrofac
-
The Gulf of Aqaba Pipeline Crossing, designed and constructed between 2002 and 2003, stands as one of the earliest deep-water developments in the Middle East region. This 15km 36” pipeline transports natural gas between Egypt and Jordan. During the design phase engineers identified and addressed potential risks, including long free spans, seismic activity and hydrotest.
Recognising the significant economic consequences of a pipeline failure, a robust Operation, Inspection, Maintenance, and Repair (OIMR) programme was established. This programme's unique strength lies in its consistency. For the past 20 years, the core operational and engineering teams, along with the inspection contractor, have ensured the pipeline's continued integrity through seven separate survey campaigns. This long-term collaboration has fostered a deep understanding of the pipeline's behaviour and enabled proactive maintenance strategies.
The OIMR programme initially planned for a rise in interventions as the pipeline aged. However, the pipeline's integrity surpassed these projections. This success can be attributed to integration of observation and analysis. As industry knowledge around deep-water pipeline spans grew, so did the accuracy of the engineering models that analyse the pipeline's behaviour. The article provides valuable insights for long-term monitoring of span fatigue damage, effects of debris on the pipeline, seabed mobility, lessons learnt in coating repair, and also gathered observations on the establishment of marine life around the pipeline in a deep-water development.
OUTLINE
• The Gulf of Aqaba Pipeline Crossing was a groundbreaking project undertaken when deepwater development knowledge was still limited.
• A robust Operation, Inspection, Maintenance, and Repair (OIMR) programme was proved to be a highly successful solution to effectively address the knowledge gaps and uncertainties.
• Insights on how the “digital twin” structural model of the pipeline is updated after each survey, and monitoring of span fatigue damage as part of a wider long term integrity management programme.
• Study of seabed mobility is important to predict freespan development and mitigation over long periods of time.
• The accumulation of debris around the pipeline can have both positive and negative impacts on the pipeline mechanical integrity.
• Monitoring of marine life development around subsea assets is very beneficial to artificial reefs studies and restoration of marine life even in deep water environment.
14:10
Technical integrity and barrier management of pipeline systems
Speaker: Helene Sirnes, Leading Advisor Pipeline & Transport Technology Pipeline Operations, Equinor
Author: Helene Sirnes, Leading Advisor Pipeline & Transport Technology Pipeline operations, Equinor
-
An extensive network of pipelines is installed in the North Sea and have been operation since mid-80’s.
Equinor has since the beginning of its existence had an internal competence centre responsible for integrity evaluations, inspection, repair, maintenance, and monitoring activities.
The transported fluids vary between multiphase, dense gas, sales gas, condensate, oil, chemicals, and CO2 injection and the pipeline portfolio consists mainly of rigid pipelines carbon steel grades X65 and X70.
This paper will discuss our maintenance philosophy and how a pipeline barrier management is applied in operation.
14:40
Novel inspection technologies with multiple detection capabilities for optimised integrity assessment of subsea pipelines, rigid risers and flexible risers
Speaker: Andreas Boenisch, Managing Director InnetiQs
Authors: Andreas Boenisch, Managing Director InnetiQs
-
Offshore pipelines and rigid risers present challenges to inline inspection. Unlike onshore distribution lines, subsea pipelines have heavy wall lines, CRA clad lines, small volumetric defect detection, multi-phase and other challenges to the standard intelligent or tethered pig technologies.
In addition to the challenges of offshore pipeline pigging, the progress in the transfer of offshore pipelines for hydrogen transportation creates a new demand for new defect detection challenges.
Based on the offshore pipeline challenges and gaps, a novel electromagnetic technology has been developed and integrated into the intelligent pig to assist in filling the known inspection gaps. The developed electromagnetic inspection technology is discussed with its technical background, capabilities and future approach to support closing the gaps in offshore pipeline inspection. The novel technical capabilities achieved with the MagControl electromagnetic NDT solution are discussed, as well as the future aspects of the electromagnetic solution for the new detection challenges that the emerging fuel lines will bring.
Flexible Risers are complex pipe configurations which at the same time are critical production assets for the offshore operations. Flexible risers limitations are mainly related to limited lifespan compared to rigid risers and potential risks associated with fatigue and corrosion. Regular inspection and maintenance are essential to ensure the safe and reliable operation of flexible risers in offshore environments. The complexity of the flexible riser walls and the variety of different type layer configurations of flexible risers demands external inspections being able to offer a variation of inspection and detection capabilities to support reliable integrity and life extension assessments.
Established and newly field integrated inspection technologies with focus of wire corrosion, -crack, -rapture and annulus flooding detection capabilities are discussed and displayed over case studies. The different NDT solutions integrated in deep water operational robotic systems are providing high resolution data for detailed information of the flexible riser condition.
The discussed selectable and adaptable inspection systems offer a systematic approach to enhance the integrity management of flexible risers, safeguarding assets, protecting the environment, and preserving the reputation of offshore operators. Through flexible, reliable, and effective inspection solutions it empowers operators to detect and address potential issues proactively, thereby minimizing downtime, mitigating risks, and optimizing the performance of flexible risers throughout their service life and beyond.
15:10
Networking break
SESSION 8: INLINE INSPECTION, MAINTENANCE AND REPAIR
15:30
Multi-year "Temporary" Isolation (– TDW SmartPlug® Isolation Technology)
Speaker: Henning Bø, Technical Authority, TDW Offshore Services AS
Authors: Henning Bø, Technical Authority, T.D. Williamson, Inc. - Stephanie Craig, Project Manager II, T.D. Williamson, Inc. and Hallgeir Foss Alsvik, Engineering Manager, T.D. Williamson, Inc.
-
The TDW inline isolation tool, the SmartPlug® tool, has achieved a significant milestone, completing a remarkable four-year isolation period.
Inline isolations are temporary, ranging from short to extended periods, typically from a few hours up to a year. However, in a recent achievement TDW completed three subsea pipeline isolations in the North Sea, extending beyond three and four years, which exceeds previous records in the history of inline isolations.
During autumn of 2019, three isolation tools, were deployed for planned duration of 2.5 years. Until their retrieval in 2023 the 12-inch, 24-inch and 30-inch isolation tools had isolated the pipelines, without any instances of isolation failure. The 12-inch and 24-inch tools were retrieved after ~3.5 years of isolation, while the 30-inch tool remained in place for four years and 10 days. As part of a field redevelopment project, the three isolation tools were employed to avoid temporary decommissioning of the pipelines during the disconnect and replacement of multiple platform topsides and reducing the consequences of failure of heavy lifting operations above the depressurized pipeline sections. The redevelopment progressed successfully with the inline isolation tools time in situ eventually reaching the four-year mark. The isolation tools underwent periodic monitoring, validating their stability and confirming the absence of changes or fluctuations in the isolated pressures.
DNV played a crucial role as the third party, involved in the qualification of the technology during engineering design review and testing. This paper details the activities leading to the execution of this groundbreaking achievement, with a focus on the 30-inch isolation tool, which currently holds the record for the longest time in situ.
16:00
Enhancing pipeline integrity and efficiency: Tethered UT wall thickness measurement with a focus on data quality and operational optimization
Speaker: Markus Ginten, Business Line Manager, ROSEN Group
Authors: Markus Ginten, Thor-Staale Kristiansen and Benjamin Kosten, ROSEN Group
-
In in-line inspection, complying with API 1163 system qualification standards is key to achieving high-quality data as a basis for sound pipeline integrity assessments. Operating within the essential variables determined in thorough test programs is crucial to maintain accuracy and reliability in data acquisition. This is applicable for conventional free-swimming inspections but also for tethered inspections often utilized for unpiggable pipelines.
This abstract highlights the importance of data quality and operational efficiency utilizing tethered Ultrasonic Testing Wall Thickness (UTWM) tools. By optimizing data quality, operators can enhance their integrity assessment process, thus mitigating risks associated with pipeline failures. Adherence to API 1163 standards not only ensures regulatory compliance but also fosters industry confidence in inspection outcomes. Additionally, this abstract emphasizes the economic benefits derived from deploying tools with higher maximum allowable tool speeds, which minimizes production loss during inspections. Through streamlined operations, operators can reduce downtime and associated costs, thereby enhancing overall profitability. In conclusion, a synergistic approach that prioritizes both data quality and operational efficiency is essential for maximizing the effectiveness of tethered in-line inspection methodologies, ultimately contributing to the sustainability and reliability of pipeline infrastructure.
16:30
Deep water pipeline repair from an ROV’s operational perspective
Speaker: Kristen Andrew Foshaug, Chief Technology Officer, Connector Subsea
Author: Kristen Andrew Foshaug, Chief Technology Officer, Connector Subsea
-
Deep water pipeline repairs are some of the most challenging operations in the offshore industry yet the market increasingly demands cost effective, simple and robust solutions solutions. The MORGRIP pipeline repair product range has a 30- year track record of pipeline repair, with an unrivalled number of these being in deep water. These include numerous worlds’-firsts – such as the first diverless rigid riser spool replacement. For extensive damages to a pipeline it is necessary to cut out and replace with a new spool section which is subsequently connected into the existing pipeline with MORGRIP Connectors. For less extensive repair scenarios or life extension measures a MORGRIP Pipeline repair clamp can be used. CSS will present a recent case study of the 32 inch MORGRIP Pipeline repair clamp with the following operational parameters: Installation depth: 2200m Test pressure 403 barg Installation angle: 30 degrees.
CSS have through many years developed pipeline repair clamps starting from an ROV’s operational perspective. This presentation will highlight reasons for major changes in design and operation when moving from diver installed to diverless installation
17:00
Chairman’s closing remarks